Where the lowest outside temperature T2 is -15 ºC, the 40 m long oil pipe DN 250 must be kept at a temperature T1 of 50 ºC. ∆T = 65 K
Heat transfer coefficient, oil to pipe wall αi = 500 W/m2 K
Heat transfer coefficient, insulation plate to air αa = 10 W/m2 K
Pipe DN 50
Inner diameter d1 = 260.4 mm
Outside diameter d2 = 273 mm
Thermal conductivity λ1 = 60 W/m K
Insulation
Insulation thickness s1 = 100 mm
Thermal conductivity λ2 = 0.06 W/m K
Aluminum insulation plate
Wall thickness s2 = 1.2 mm
Thermal conductivity λ3 = 200 W/m K
Calculation objective:
Heat loss
of the pipe

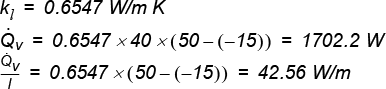
In order to keep the oil pipe at 50 ºC when the outside temperature is -15 °C, compensation of 1702.2 W (42.56 W per running meter) is required from the trace heater tracer pipe.